Disc brakes have been known for a long time. They have proven themselves well and are now used very widely. But first things first.
Currently, there are two types of braking systems – drum brakes and disc brakes. For the first time disc type brakes were applied in the late 40’s of XX century, and since the 70’s drum brakes on the front wheels were replaced by disc brakes on all cars.
We have established reliable partnerships with Bobcat dealers allowing prompt supply of both genuine spare parts and certified will-fit parts. Select Bobcat spare parts via AGA Parts web-catalog.
This article will give a detailed description of disc brakes, their advantages over their drum counterparts, as well as a description of the components of this braking system (caliper, brake disc, protective shield). In addition, the advantages and disadvantages of different types of disc brakes are described.
Advantages of disc brakes over drum brakes
The advantages of disc brakes over drum brakes are as follows:
- the stopping power of disk systems is not reduced by overheating because they are better cooled;
- the resistance of disc brakes to water and contamination is higher;
- the brake requires much less maintenance;
- The friction surface of disc brakes is greater than that of drum brakes for the same weight.
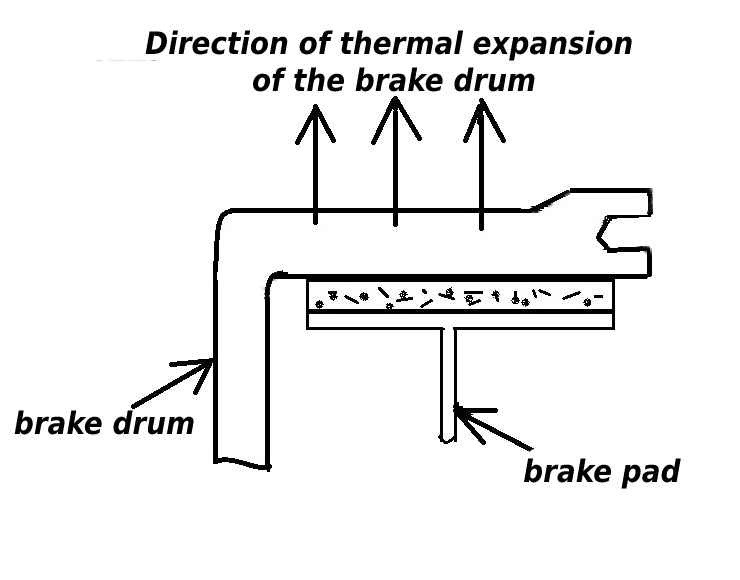
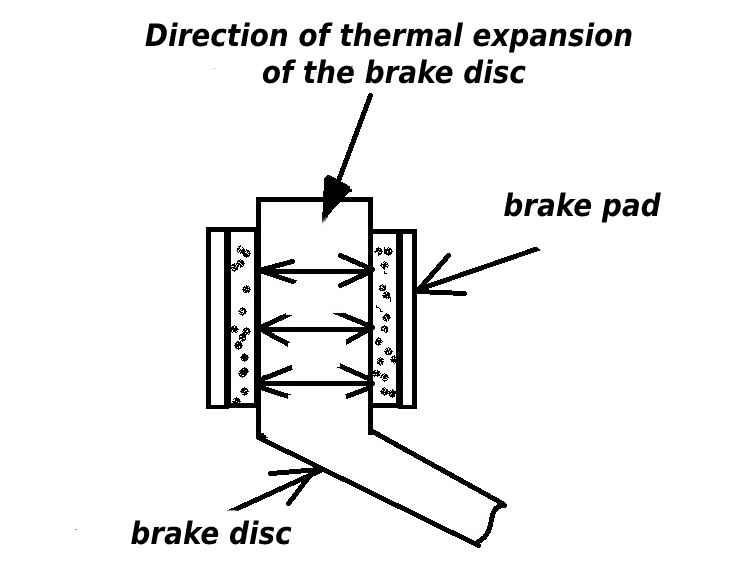
When the brake drum heats up, the thermal expansion of the brake drum – an increase in internal diameter – causes the brake pedal travel to increase or the drum to deform, which can cause a dramatic reduction in braking performance (pic 1). The brake disc, in turn, is a flat part, its thermal expansion occurs toward the friction material, so compression of the disc cannot cause deformation sufficient to affect the braking performance. In addition, the centrifugal force will bounce contaminating materials away from the brake disc to the outside.
Picture 2 shows why a disc brake cools better than a drum brake.
The cooling air only begins to cool the brake drum once the heat generated by braking has passed through its walls, while the rubbing surfaces of the disc brake are open to air. Heat transfer from the brake disc to the air begins immediately after the brakes are applied.
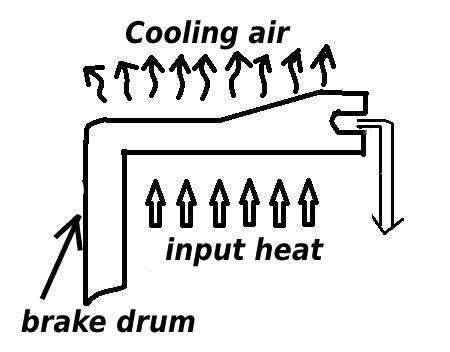
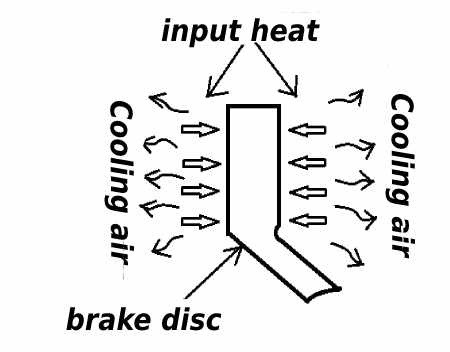
The ability to adjust disc brakes is another advantage of them. The projection of disc brakes is such that they self-adjust after each use due to the small gap between the pads and the brake disc.
Disc brake construction
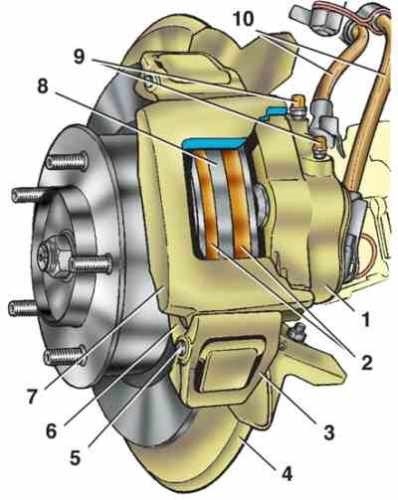
1 – cylinder block;
2 – brake pads;
3 – caliper clamping arm;
4 – protective cover;
5 – axle of pressure arm;
6 – pad guide;
7 – brake caliper;
8 – brake disc;
9 – sockets for air removal;
10 – brake hoses,
The main parts of disc brakes are the caliper, brake disc, pads, shield. Let’s consider these elements of the braking system in more detail.
Disc brakes are divided into single and multi-disc brakes. Their largest and heaviest part is the brake disc. The mechanism of operation of single-disc brakes is reduced to the fact that the brake pads with friction material during braking clamp one brake disc. Multi-disc brakes, usually used in aviation, have several rotating brake discs, separated by fixed discs (stators). The brake shield of multi-disc brakes contains hydraulic cylinders and pistons that control the brake pads and clamp the brake discs and stators when extended. Multi-disc brakes are made entirely of metal, while single-disc brakes consist of organic and metal friction material.
The brake disc material, like the brake drum, is usually cast iron. Cast iron has good wear resistance and good frictional properties, has high hardness and strength at high temperatures; it is easily machinable, and its cost is relatively low.
The size of a brake disc is equal to its outside diameter and the total cross-sectional thickness between the two working surfaces. The diameter of the brake disc is usually limited by the size of the wheel, and a vented brake disc is always thicker than a solid disc. For a disc brake, it is the total area of contact with the two brake pads in one disc rotation.
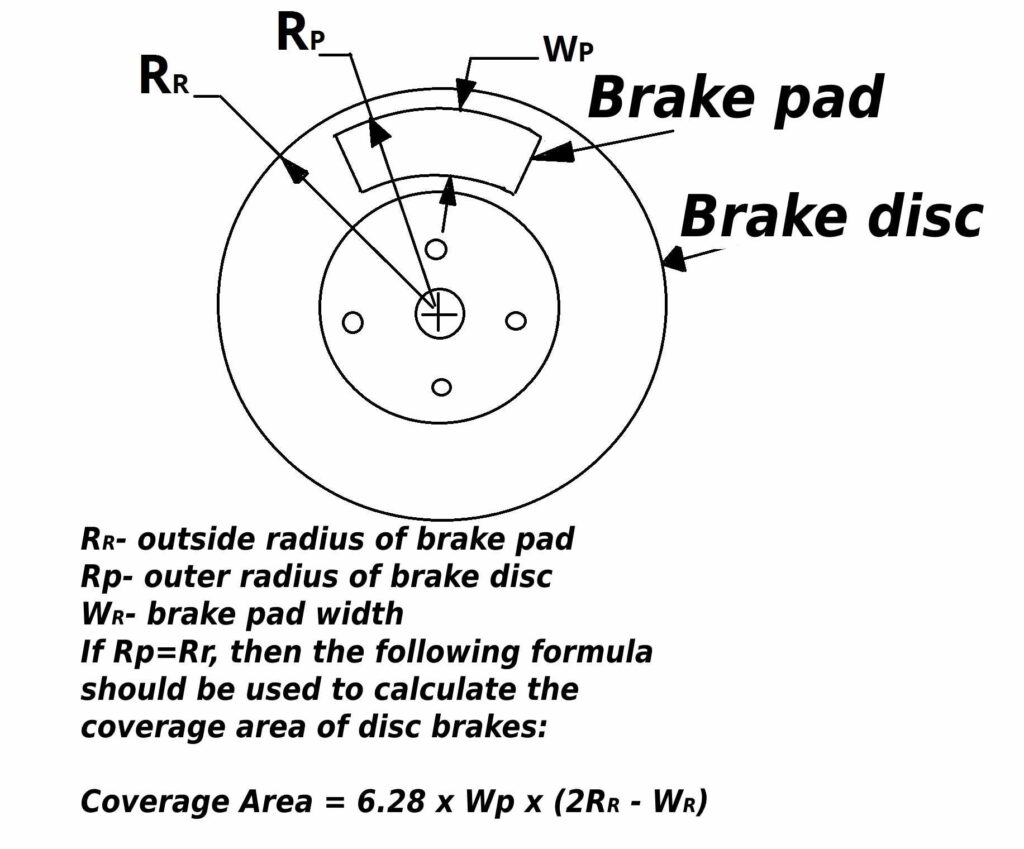
A high ratio of area coverage per tonne of vehicle in well designed brakes means that the braking system is highly efficient. The coverage area of a disc brake is the friction area of the brake pads on both sides of the brake disc. Thus, it is more accurate to use Rp instead of Rr, but since in most brakes both radii are nearly equal, Rr, which is easier to measure, is used for ease of calculation.
The brake disc is attached to the spacer, which in turn is attached to the wheel hub or axle flange. The spacer provides a longer path for heat transfer from the rubbing surface of the brakes to the wheel bearings, which keeps their temperature quite low. Production car spacers are usually made of cast iron as one piece with the brake disc, while racing car spacers are made as a separate piece of aluminum alloy. The disadvantage of aluminum alloy spacers is a higher thermal conductivity than cast iron, which leads to more heat in the wheel bearings.
Ventilated disc brakes
The brake disc can be solid or with ventilation channels inside it. Solid brake discs are usually used in light vehicles. Ventilated brake discs with radial cooling channels are used on heavy vehicles that require the largest possible disc sizes.
High-powered racing cars are equipped with ventilated brake discs, and there may be differences in the thickness of their side walls. To ensure that the temperature on each side of the brake disc is the same, on many racing car brakes the side of the brake disc closest to the wheel is thinner than the opposite side. The wheel resists the passage of cooling air to the outside working surface of the brake disc, making it hotter than the inside, so the greater thickness of the poorly cooled outside surface of the brake disc helps equalize their heating temperatures.
Race car brake discs often have curved cooling ducts that increase the efficiency of the airflow. Brake discs for left and right side cars are not interchangeable due to the curvature of the air vents. A brake disc with curved vents or slanted slots must rotate in a certain direction to work effectively. The correct direction of rotation in relation to the vents and slots is shown in the diagram.
Typical values for specific brake coverage area are shown in the table for typical 1981/82 cars.
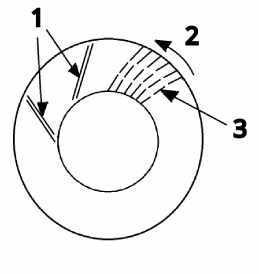
2 – disc rotation direction
3 – curved ventilation holes
Typical values of specific brake coverage area per ton of vehicle weight
Car model |
Alfa Romeo Spyder |
Audi 5000 Turbo |
Audi Quattro |
BMW 528e |
Chevrolet Camaro Z28 |
Chevrolet Corvette |
Dodge Charger 2.2 |
Ferrari 308GTSi |
Ford Mustang GT 5.0 |
Honda Accord |
Honda Civic |
Lamborghini Jalpa |
Mazda GLC |
Mercedes-Benz 380SL |
Car model | |
Mitsubishi Lynx RS | 1212,6 |
Nissan Sentra | 1754,4 |
Peugeot 505 STi | 1735,05 |
Pontiac J2000 | 1115,85 |
Porsche 944 | 1954,35 |
Renault Alliance | 1225,5 |
Renault 5 Turbo | 1128,75 |
Renault 1,8i | 1219,05 |
Subaru GL | 1090,05 |
Toyota Celica Supra | 1444,8 |
Toyota Starlet | 1264,2 |
Volkswagen Scirocco | 1277,1 |
Volkswagen Scirocco SCCA GT3 | 1960,8 |
Volvo GLT Turbo | 1560,9 |
*Powerful cars have higher values of this indicator compared to economical sedans.
Possible malfunctions of disc brake systems
Ventilated disc brake discs develop cracks if they are subjected to frequent heavy braking. This is caused by thermal stresses and brake pad pressure on the thin metal walls in each cooling duct. Thermal stresses in a brake disc with a molded or bolted-on spacer are caused at the joint because the temperature of the brake disc at this location is higher than the temperature of the spacer.
The outside of the brake disc expands more than the cold spacer as it heats up. This causes the brake disc to warp and bend, taper and cause uneven wear on the brake pads. By constantly repeating, the expansion and contraction of the brake disc causes it to crack. Supporting each side of a vented brake disc and cooling it effectively reduces the chance of cracking the disc.
Brake drums and brake discs are designed to withstand the heaviest version of thermal stress with each brake application, but repeated brake applications can cause fatigue cracking. If brakes are used in hard braking applications, they should be checked more often.
Disc Brake Calipers
Let’s take a closer look at the construction of calipers. Disc brake calipers include brake pads and hydraulic brake cylinders with pistons that press the pads against the brake disc. The principle of all disc brake calipers is the same: when the driver presses the brake pedal, the pressure of the brake fluid moves the pistons to move the brake pads, which clamp the brake disc.
Car brake calipers are usually made of relatively cheap, high-strength, spheroidal graphite gray cast iron. However, they are quite heavy. Racing or generally high-powered cars are usually equipped with aluminum alloy calipers, and they weigh about half as much as cast-iron calipers.
Calipers types and their features
There are two main types of calipers – fixed and floating.
Fixed calipers have more pistons (two or four), are larger and heavier than floating calipers. In heavy-duty applications, they allow more emergency braking before the caliper overheats.
Floating calipers move in the opposite direction of the piston movement. Because the floating caliper only has a piston on the inside of the brake disc, the entire caliper can move inward so that the outer brake pad can press against the brake disc. Floating calipers are less prone to leakage and wear because they have fewer moving parts and seals.
Fixed calipers are most commonly used on race cars and floating calipers on production cars.
The advantage of floating calipers is the ease of application of the mechanical parking brake, since in a single brake cylinder design it is easily controlled by a cable, while in fixed calipers with pistons on both sides of the brake disc it is more difficult to do so. The disadvantage of floating calipers is that they can cause uneven wear of the brake pads due to movement of the caliper itself.
Possible caliper failures
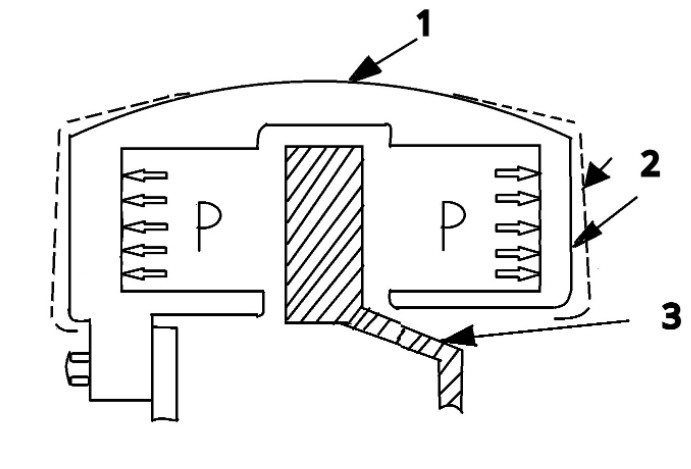
1 – Bridge
2 – deformation under the force P
3 – brake disc
- The part of the caliper body that covers the outer diameter of the brake disc is called the axle. The pressure of the brake fluid causes a force P to act on each side of the caliper, which tries to bend its axle. The stiffness of the axle determines the stiffness of the entire caliper structure, as the cross-sectional thickness and weight of the caliper depend on the stiffness of the structure.
- The caliper sits between the outer side of the brake disc and the inner side of the wheel disc, so the space requirements to accommodate it dictate designing a caliper with a small cross-sectional thickness. Unfortunately, this can cause it to bend. To increase stiffness, race car brake calipers are designed with wide axles.
- If the brake pad overlaps the dimensions of the piston, it will bend when the brakes act. Multiple pistons are used to ensure even contact between the working surface of the brake pad and the brake disc.
- If the caliper mounting hardware is malleable, torsion may occur when the caliper is moved, which in turn causes uneven wear on the brake pads, springiness, and increases the travel of the brake pedal.
- Since the brake disc and caliper bracket are in different planes, the latter perceives torsional torque while the brakes are applied. If the bracket is too thin, it will twist, causing the caliper to catch on the brake disc. Normally, the caliper mounting bracket should be at least 12.7 mm thick.
Operating particularities of disc brake systems
Brake shields are installed to protect the inside of the operating side of the brake disc from dirt and water. Such a device is similar in design to the brake shield of drum brakes. The guards block the flow of cooling air to the brake disc and are therefore not normally installed on disc brakes for racing cars.
As for disc brake friction material, it is usually glued to the side of the brake pads, which are made of steel plate. Brake pads are sold with brake pads already attached; they are not reused.
The load from the brake pad is not normally applied directly to the piston in the brake caliper. On many vehicles, anti-squeaking washers are installed between the piston and brake pad to reduce the noise that occurs when the pad vibrates or rattles against the brake disc.
To summarize
We have considered the structure of disc brake systems, features, advantages, strengths and weaknesses of their different types. From all of the above, it is not difficult to draw conclusions about what should be the most effective braking system for racing cars.Only ventilated brake discs, which cool faster, are suitable for racing cars. To keep the temperature on each side of the brake disc the same, on many race car brakes the side of the brake disc closest to the wheel is thinner than the opposite side. Curved brake disc vents are more efficient for racing cars than straight ones. Compared to a traditional straight vent design, the directional vent holes greatly increase the airflow through them, improving heat dissipation. The spiral design of the channels distributes mechanical stresses more evenly throughout the disc, increasing life and reducing the chance of cracking.
- Disc perforations, while providing the same gas-transfer function as the channels, increase disc surface area to be blown for improved cooling. In year-round operation, it improves disc cleaning from moisture and dirt.
- Disc brake spacers and calipers for racing cars – made of aluminum alloy. The lightweight aluminum spacer improves handling characteristics and reduces thermal stresses on the brake disc. The low weight, due to the use of aluminum with a low specific gravity, reduces the unsprung masses, favoring the quality of the car’s suspension.
- The fixed caliper, designed for more emergency braking and with more flexibility than the floating caliper, is ideal during racing.
- Increased width axles provide sufficient stiffness of the disc braking systems for race car operation. Thanks to the enlarged and better distribution of the “axle” cross-sections (the element working on the expanding caliper loads) the caliper’s stiffness to working deformations is increased. Increased rigidity, combined with the overall reduction of operating pressures and reinforced by the brake hoses, which have a minimal tendency to increase in volume (swelling) under load, allows for maximum information on the brake pedal and the ability to very precisely dosed brake torque in the system.
- Multipiston caliper design allows to get uniform pressure force of a brake pad to a disk, and different diameter of pistons compensates a difference of temperature conditions of work of a pad on the contact area, preventing possible uneven wear (taper) on the front and back edges. Increased total piston area in the calipers, changes the transmission ratio of the hydraulic system, resulting in significantly lower fluid working pressures. Lower pressures reduce the maximum brake pedal force required. Reduces stress and detrimental strain on all conventional parts of the brake system.
- With a “floating disc design” recommended for extreme load applications (racetrack), allows complete removal of thermal stresses relative to the center section and prevents the transfer of excessive heat to the hub bearing. Ensuring proper operation and extended life of these parts in the harshest conditions.
- The larger the diameter of the brake disc, the larger the effective radius of application of the braking torque. This increases the maximum braking power to be delivered by the system. The effective radius directly affects the effective surface area, which is one of the most important indicators of a disc’s ability to dissipate thermal energy.
And remember, quality disc brakes are first and foremost about your safety. Keep this in mind when choosing the right brake system for your car.
Comments are closed.